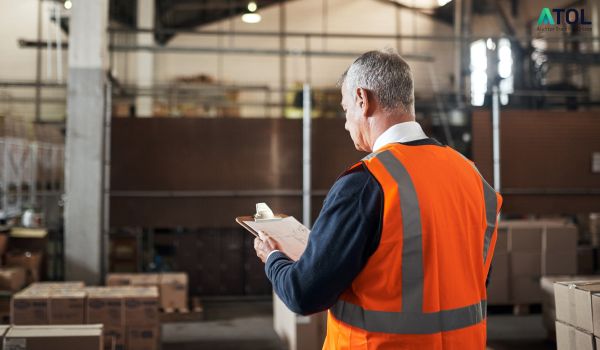
This article covers clause 8.7 Control of nonconforming outputs. This clause is going to be broken down and turned into something you can all understand and implement in your own organization or industry. Keep on reading as I can show you just how easy this is!
This clause starts off with subclause 8.7.1 stating:
The organization shall ensure that outputs that do not conform to their requirements are identified and controlled to prevent their unintended use or delivery.
Ok, let’s stop there and confirm what this means before we move on further.
This is just saying that we are required to identify when we have produced our product or service and it does not meet the customer or other interested parties requirements. When we do identify it, we need to take action to control it so that we stop it from happening again.
Now let’s move on to the next part of this clause which states that:
The organization shall take appropriate action based on the nature of the nonconformity and its effect on the conformity of products and services. This shall also apply to nonconforming products and services detected after delivery of products, during or after the provision of services.
And then to help us even more the clause gives us a list of what these appropriate actions could be, so let’s work our way through this one by one. The clause states that:
The organization shall deal with nonconforming outputs in one or more of the following ways:
a) correction;
Ok, this is simply fixing it.
If we have had a product or item that was manufactured and was meant to be painted green, however it came out red, we could put it back through the machine or the process and paint it green - that’s a correction. Of course, we would only select this option if we could repaint the item and it didn’t impact the functionality of the item.
Then we move on to the next option which is:
b) segregation, containment, return or suspension of provision of products and services;
Now we have this red product or item that is not conforming because it was meant to be green. We are not able to repaint it (as in my first example) because it would impact the functionality of the product, so our option then is to segregate or contain the item – this means we would quarantine it, and even possibly tag it, so it is not used or sent out to a customer.
The next option this clause gives us is:
c) informing the customer;
So, of course, if our customer specifically requested this product to be green and we are not able to repaint it again, we would communicate this to the customer so they are kept in the loop of what the corrective action will be which does lead into point d;
d) obtaining authorization for acceptance under concession
This means that possibly the customer is ok with the product being red instead of green. It doesn’t really impact the use of the product and they are happy to accept it under concession.
In this instance, they might receive a discount or a credit for goodwill and customer relations. But the point is that the customer will take possession of the item even if it doesn’t meet their initial requirements.
You may find that some of these options are relevant to your products or services and some are not. And remember these nonconformities could be detected before the product is sent to the customer or after – regardless of the timeframe for identification, the same options are to be considered.
Then the next and final statement in this subclause of 8.7.1 states that:
Conformity to the requirements shall be verified when nonconforming outputs are corrected.
Meaning that when you do take action to rectify or correct a nonconformity, you should check that the product or item continues to meet all of the requirements – again. So, if you are able to repaint the red product green, then all of the normal quality checks at this point are to be followed. Nothing changes.
We then move on to the second subclause of 8.7.2 which states that:
The organization shall retain documented information that:
a) describes the nonconformity;
b) describes the actions taken;
c) describes any concessions obtained;
d) identifies the authority deciding the action in respect of the nonconformity.
We need to retain some evidence of any nonconformities that are identified.
This is normally something that is maintained in a Nonconformance Register or Improvement Register – you can call it what you want really. This register should include what the nonconformity was, what actions were taken (remember from correction, segregation, informing the customer or acceptance of the product under concession as explained already), and finally who is authorized the final action or actions to be taken.
If you maintain a register then this is perfectly fine to meet this documented information requirement and don’t forget it helps you to monitor and analyse your nonconformances and improve your systems, which is ultimately what we want to achieve, isn’t it?
Now that you have a better understanding of these requirements, it's time to take action and implement them in your own organization and ISO 9001 quality management systems.
If you prefer watching over reading, head to our ATOLTV ISO 9001 playlist on YouTube. And if you're interested in becoming an ISO 9001 specialist, check out our range of ISO 9001 quality management systems courses and qualifications today.